We use cookies to make your experience better. To comply with the new e-Privacy directive, we need to ask for your consent to set the cookies. Learn more.
TEST
Milling Bur System
Overview
The Bredent Three Step Milling system consists of 3 burs of the identical shape, but each designed for different surface finishing. This will allow you to drastically cut finishing time by giving you the capability to precisely pre-mill in the wax stage. After casting, the metal milling bur is used to do the final finishing. This metal bur is exactly the same shape as the wax bur which minimizes the milling time required on the metal. The final high shine polish is achieved with the polishing bur. Using this system, you can save costs, time and material.
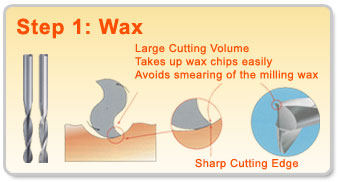

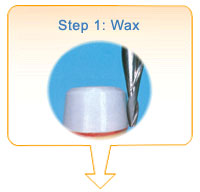
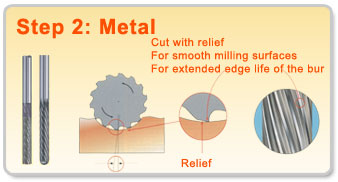

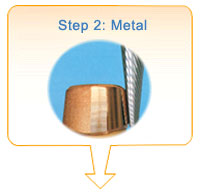
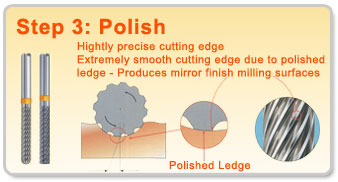
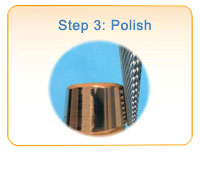
Groove Burs
The groove bur exclusively serves to prepare grooves. For this purpose the groove bur is only moved up and down in the vertical axis. The cut on the face simplifies extending the grooves to the cervical direction. At speeds of 15,000 - 20,000 rpm a fine cutting performance and a mirror-like high luster on the milling surface are obtained.
Shoulder Burs
The occlusal shoulder is prepared with a special shoulder bur. The shoulder bur features a face cut which smoothens the bottom of the shoulder. Optimum use of this tool is ensured at speeds of 15,000 - 20,000 rpm. A mirror-like luster on the milling surface is achieved with the relief cut. Additional polishing is not required.
Non-Precious and Titanium
A rich quantity of milling and drilling oil is applied onto the milling surface and a speed of 20,000 - 25,000 rotations per minute is used for milling. While adding a copious amount of milling and drilling oil, the milling surface is prepolished with the polishing bur at 20,000 rotations per minute and then polished to high luster at 10,000 rotations per minute.
The cutting edge geometry has been especially designed for rapid removal of material. The relief ensures smooth running and allows very smooth surfaces on the object to be milled. The wide relief extends the edge life and avoids breaking of the sharp cutting edges.
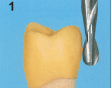
It is recommended to wax the entire crown in wax prior to starting the milling work.
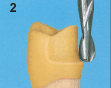
In the first step a shoulder with a margin step is prepared with a round 2.3mm parallel wax bur.
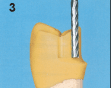
The insertion grooves are then prepared with the flat 1.0mm groove bur.
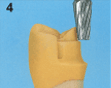
The final wax step is to mill an occlusal shoulder with the 2.7mm shoulder bur.
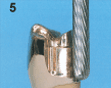
After casting the crown, the parallel surface is finished with the 2.3mm round metal bur.
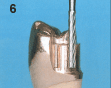
The insertion groove is finished with the same groove bur. The bur should only be moved up & down in the vertical axis.
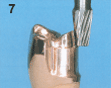
The occlusal shoulder is reworked with the 2.7mm shoulder bur.

Finally, a high luster is achieved on the parallel surface using the 2.3mm round polishing bur.
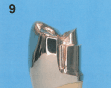
The bredent milling burs produce such a high shine that additional polishing is not needed..
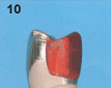
A secondary element with anatomy is created with the Pi-Ku-Plast pattern resin. (Pg. 115 and 116)
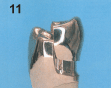
The secondary element is cast and fitted onto the crown.
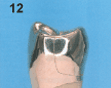
The low shrinkage of the Pi-Ku-Plast pattern ensures excellent precision of fit of the two pieces.